MAMMOBOT
King's College London
2022

The Problem
Existing designs of soft-growing robots, including the millimeter-scale MAMMOBOT, grapple with issues concerning sensor placement at the tip of the robot, and the risk of detachment during operation, necessitating a more efficient solution. The MAMMOBOT, a flexible robot operating at the millimeter scale, introduces additional complexity, as ethical concerns surrounding the use of specific materials within the body raise critical issues of potential contamination and stability, compelling the exploration of innovative approaches to address these challenges.
The central issue revolves around the continual movement of material at the robot's tip as it undergoes dynamic "growth" and maneuvers. Conventional sensor mounting becomes impractical due to the fluid nature of the robot's body, necessitating a solution that seamlessly moves in tandem with the robot's motion. To meet the demands of the robot's "growing" capabilities and its need for versatile movement, we tackled the complexities of designing a solution that accommodates retraction, turning, and navigating through confined spaces.
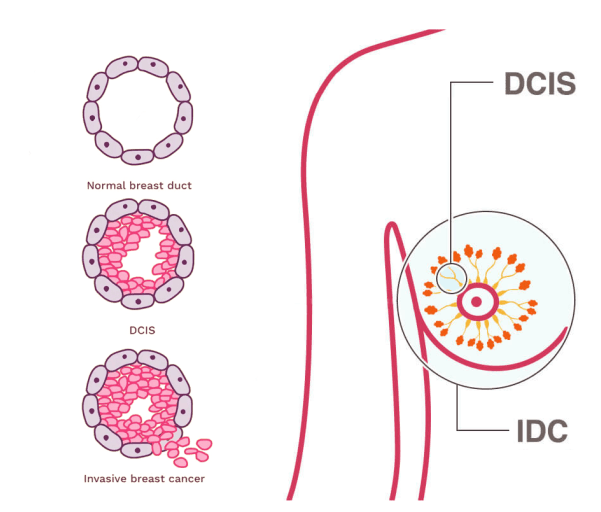
Proposed solution
The devised solution integrates pressure sensors linked to an Arduino, providing real-time obstacle detection along the robot's path. The top section of the 3D-printed tip incorporates sufficient space to accommodate the plastic material's growth and facilitate the forward movement of the tip. To ensure consistent positioning at the apex of the robot, a secondary 3D-printed component is introduced inside the robot. The strategic use of magnets unites these two 3D-printed parts seamlessly, creating a cohesive unit that empowers the robot to navigate its surroundings effortlessly, without external assistance.
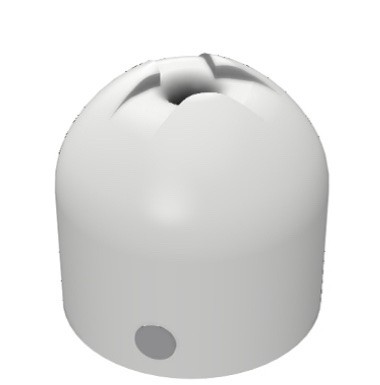

In order to enhance the testing procedure, I revamped the method by which the robot undergoes growth. Establishing a standardized testing setup was crucial to ensure the tests were conducted promptly and consistently. Typically, soft-growing robots require a reel of material for the robot's body to be contained within an enclosed chamber, which is then pressurized. When the robot needs to advance, a motor unwinds the reel, facilitating the growth of the robot. The redesign involves relocating the reel outside the pressurized chamber, allowing for a larger material reel and the potential passage of wires and various other equipment.
The plastic reel is threaded through the bottom hole, flipped around, and secured at the top. At the upper section, threads and a nut facilitate easy insertion and removal of the plastic as needed, securely holding it in place against any tape or adhesives. On the right side, a small notch in the 3D-printed housing accommodates a pressure sensor for monitoring internal pressure. On the left, a specialized locking mechanism enables the attachment of the 3D-printed part to an air pump, used to pressurize the robot's body.
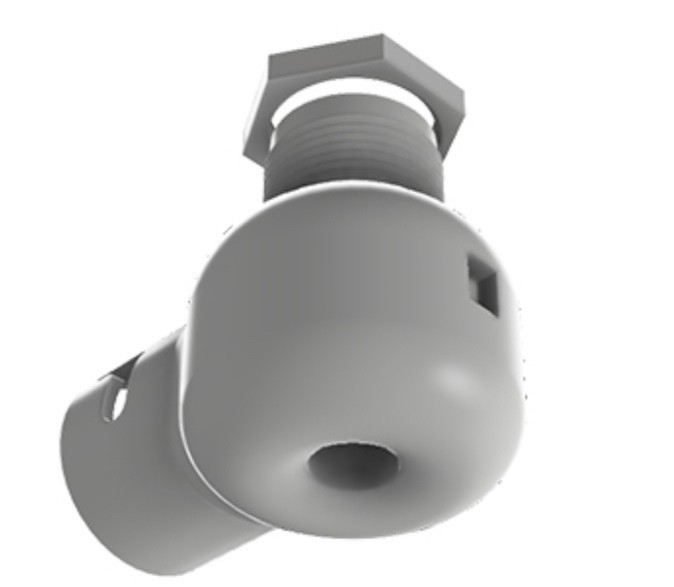
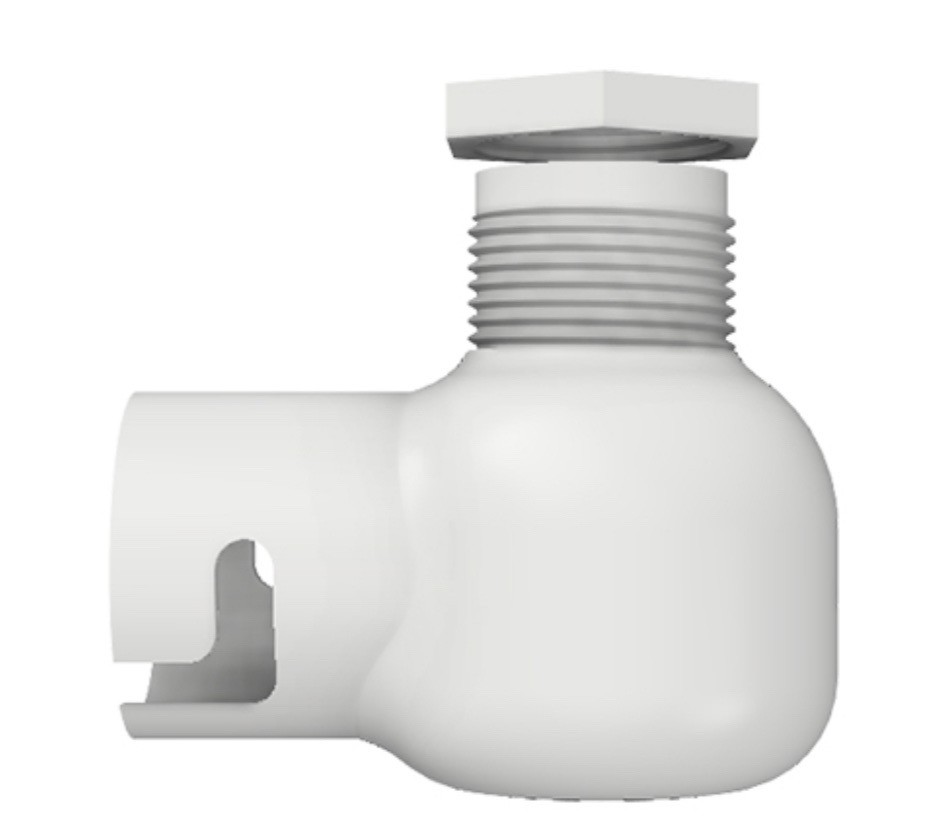
Moreover, I constructed a platform designed to accommodate the air pump, reel, and Arduino for sensor value readings. This platform provided the flexibility to move the prototype conveniently within the lab, and reduced the chances of mistakes and loose connections. Furthermore, the platform is equipped with buttons, offering the capability to control the robot's movement both backward and forward as required.

Ultimately, the graph presented below illustrates the pressure sensor readings as the robot's tip encounters an obstacle. The initial contact with the obstacle is denoted by the prominent blue spike, while the subsequent green segment signifies the robot's turn, accompanied by a gradual decrease in pressure on the sensor. During the phase where the robot glides against the obstacle, the pressure sensitivity remains consistently flat. Notably, the detection of a minor bump on the obstacle is represented by a smaller red spike.
